- +86 18825289328
- support@hiwonder.com
- Home
- Servo & Controller
- Hiwonder Serial High Voltage Bus Servo HTS-21H Anti-burning and Anti-blocking Intelligent Serial Port High Torque High Precision with Feedback Dedicated for Robot Gripper Claw Hiwonder Serial High Voltage Bus Servo HTS-21H Anti-burning and Anti-blocking Intelligent Serial Port High Torque High Precision with Feedback Dedicated for Robot Gripper Claw
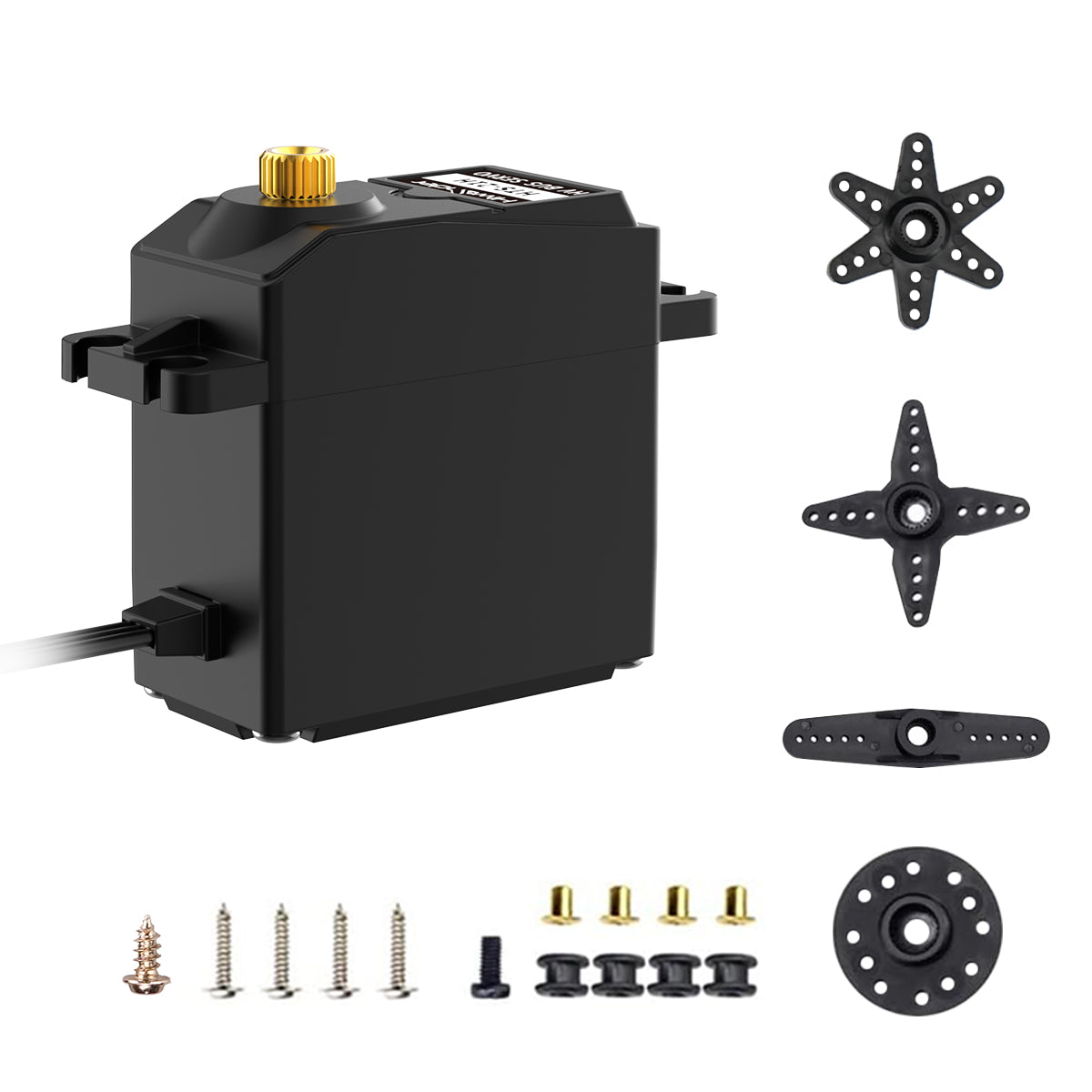
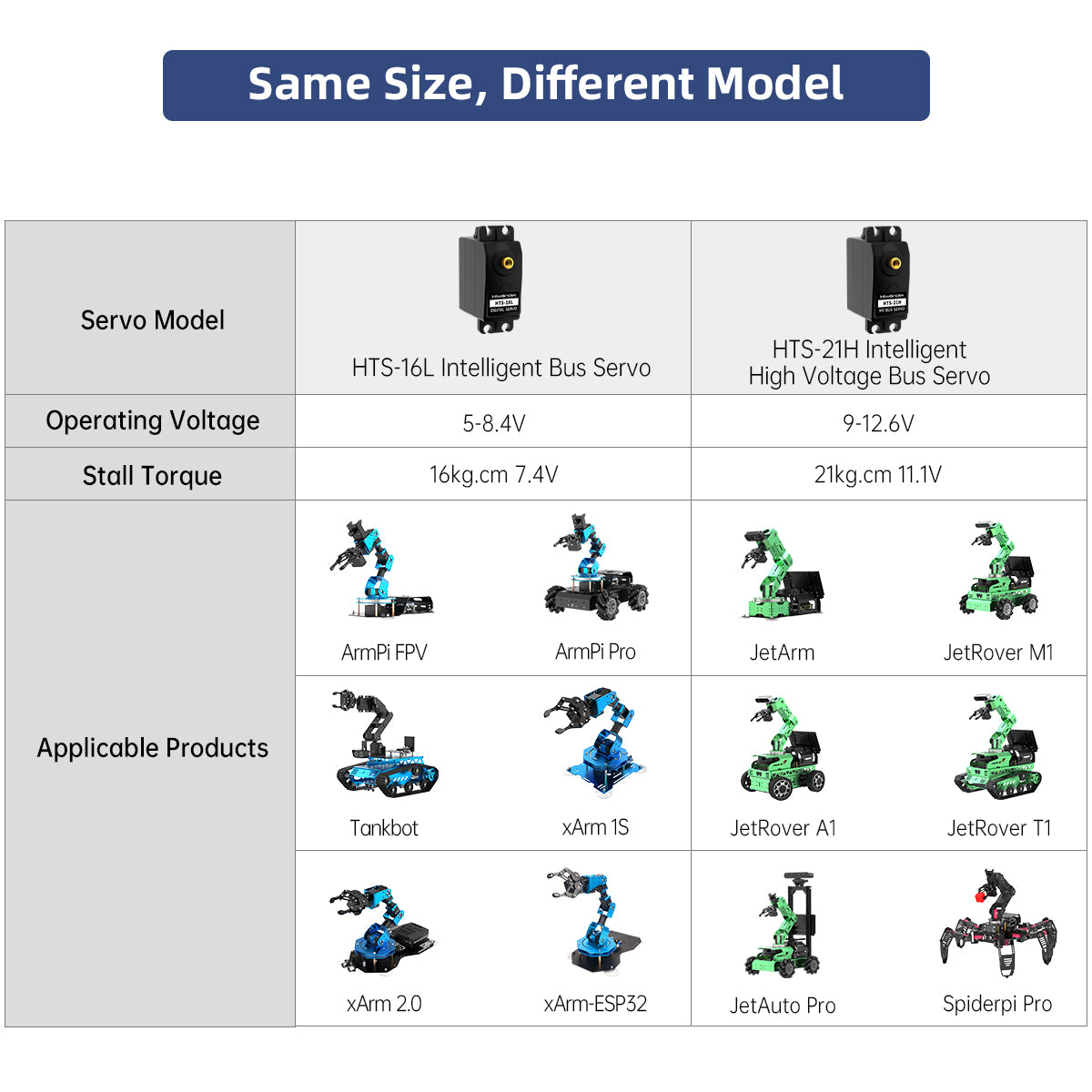
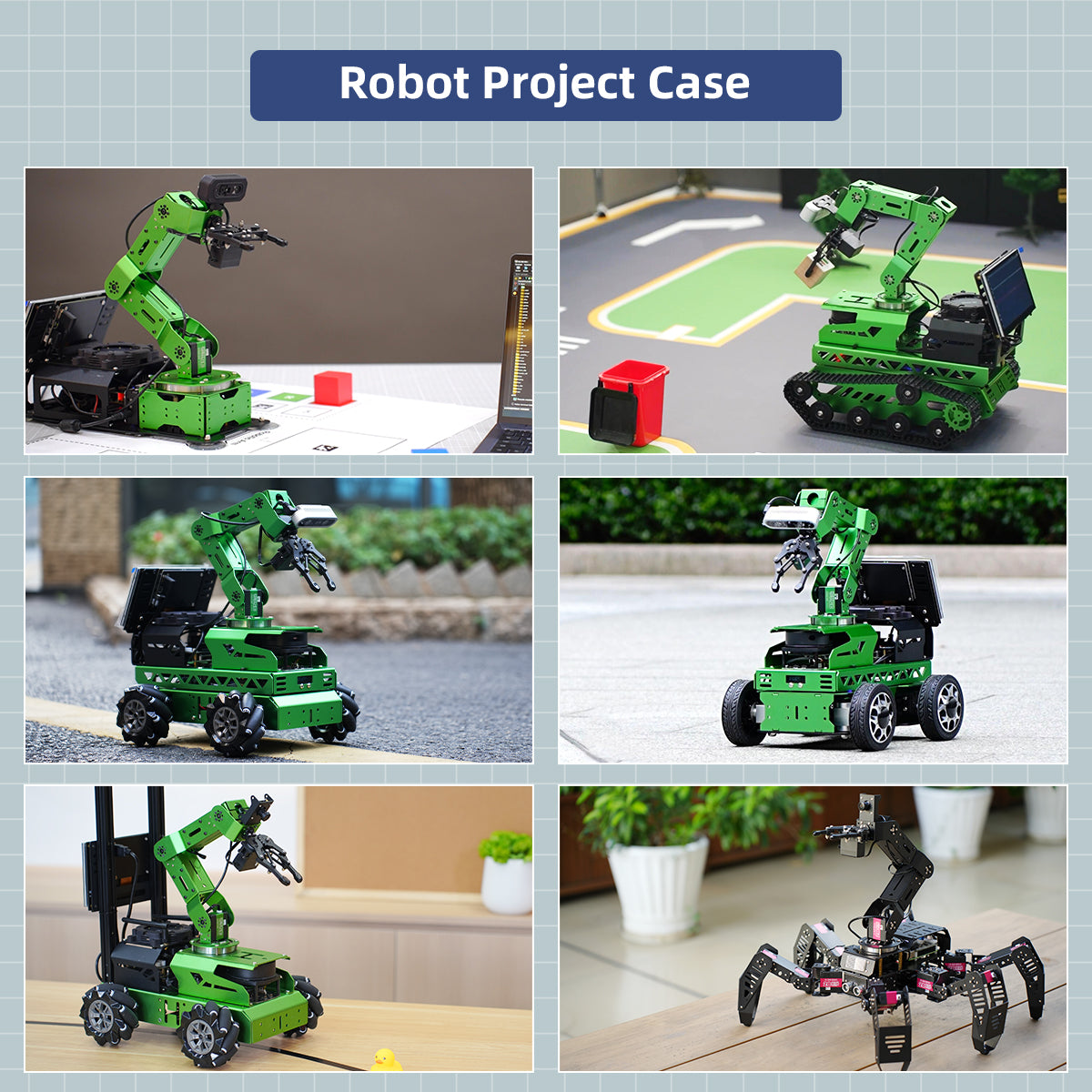
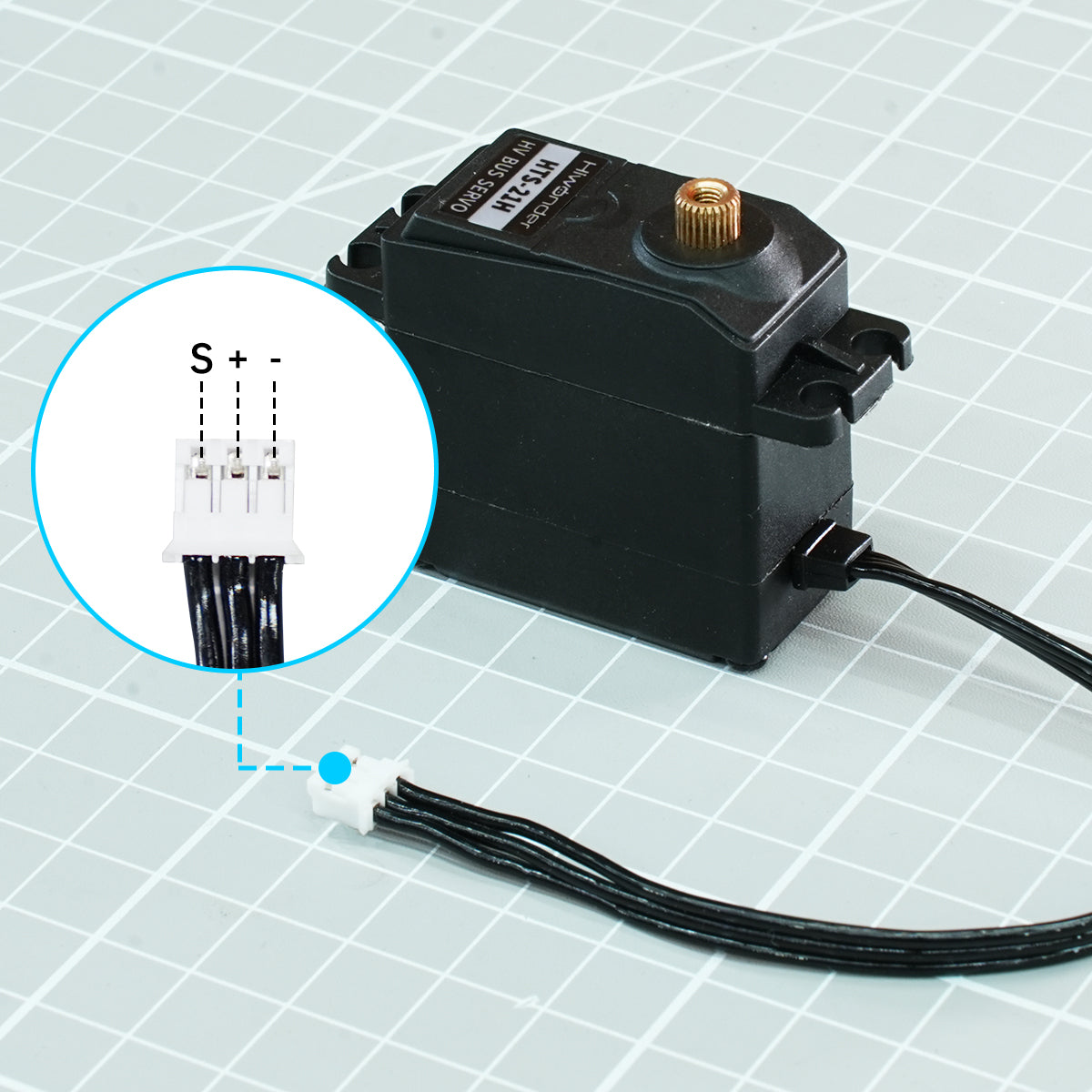
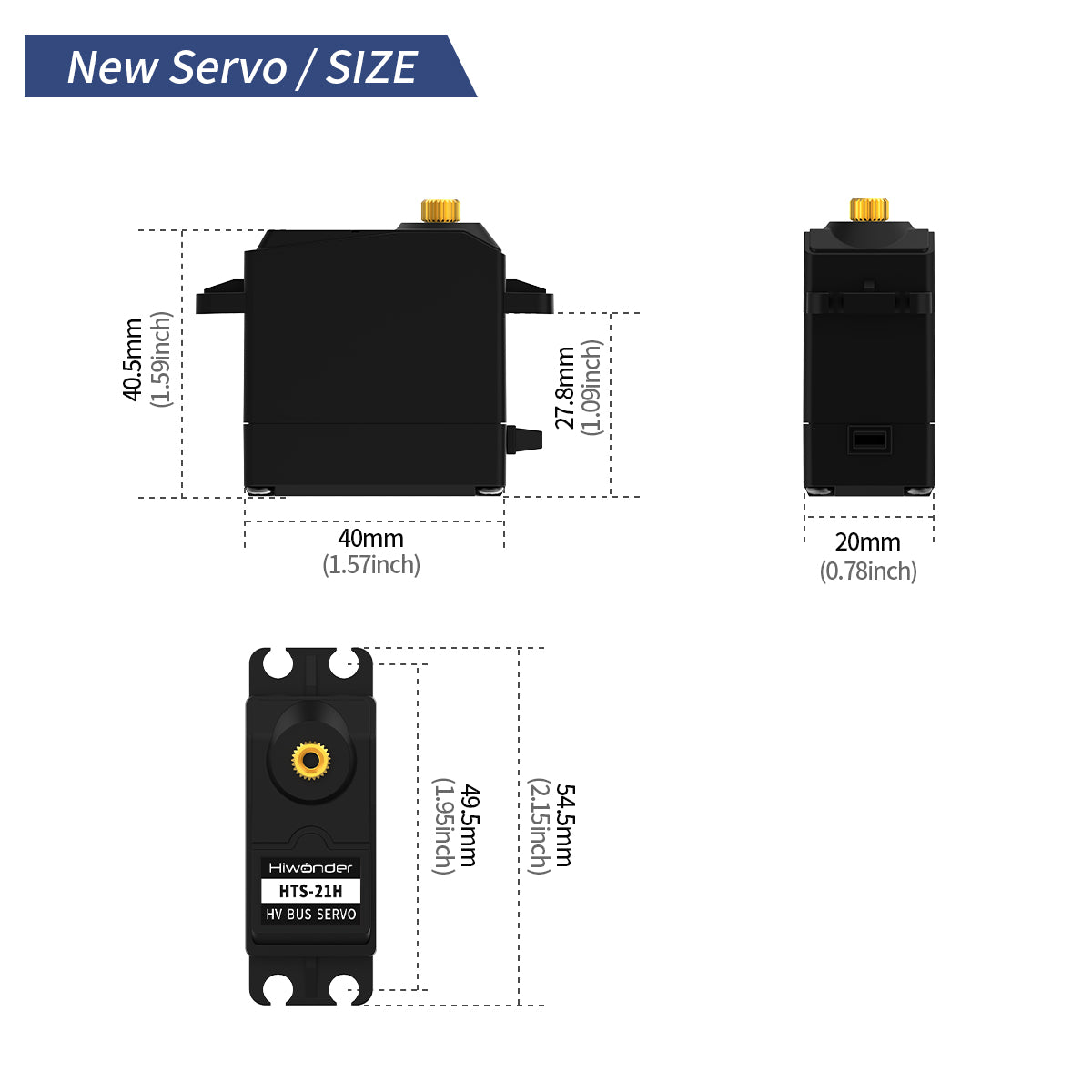
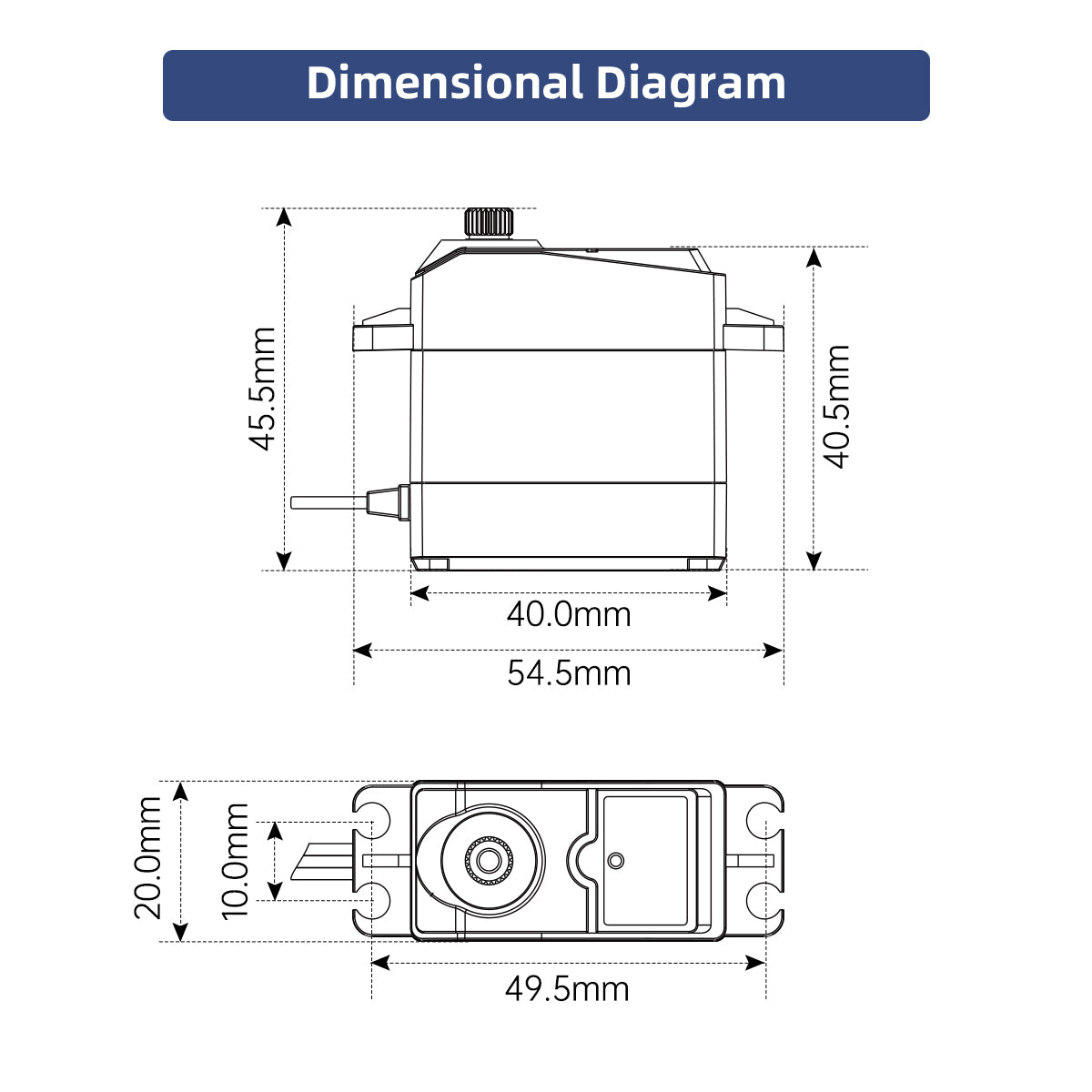
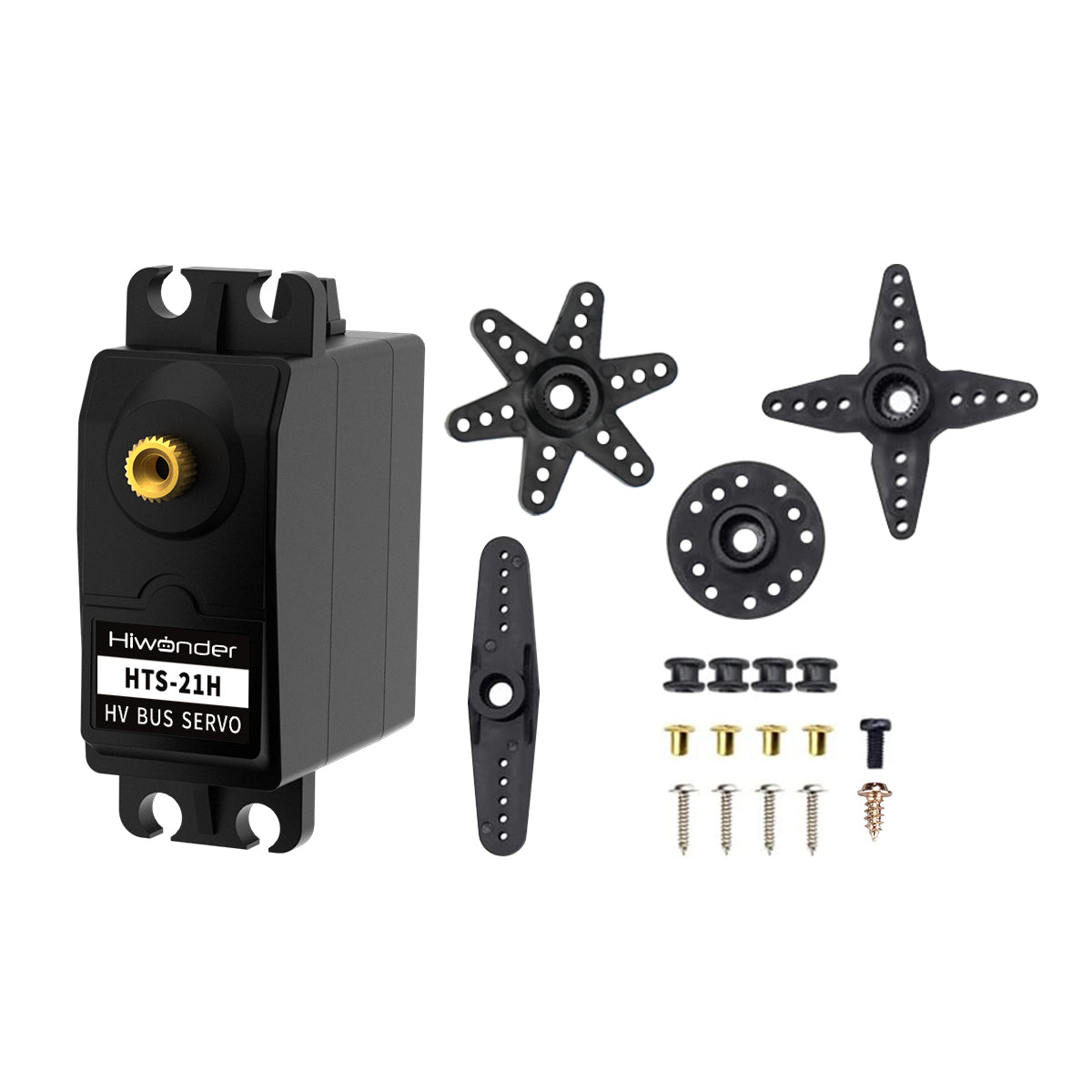
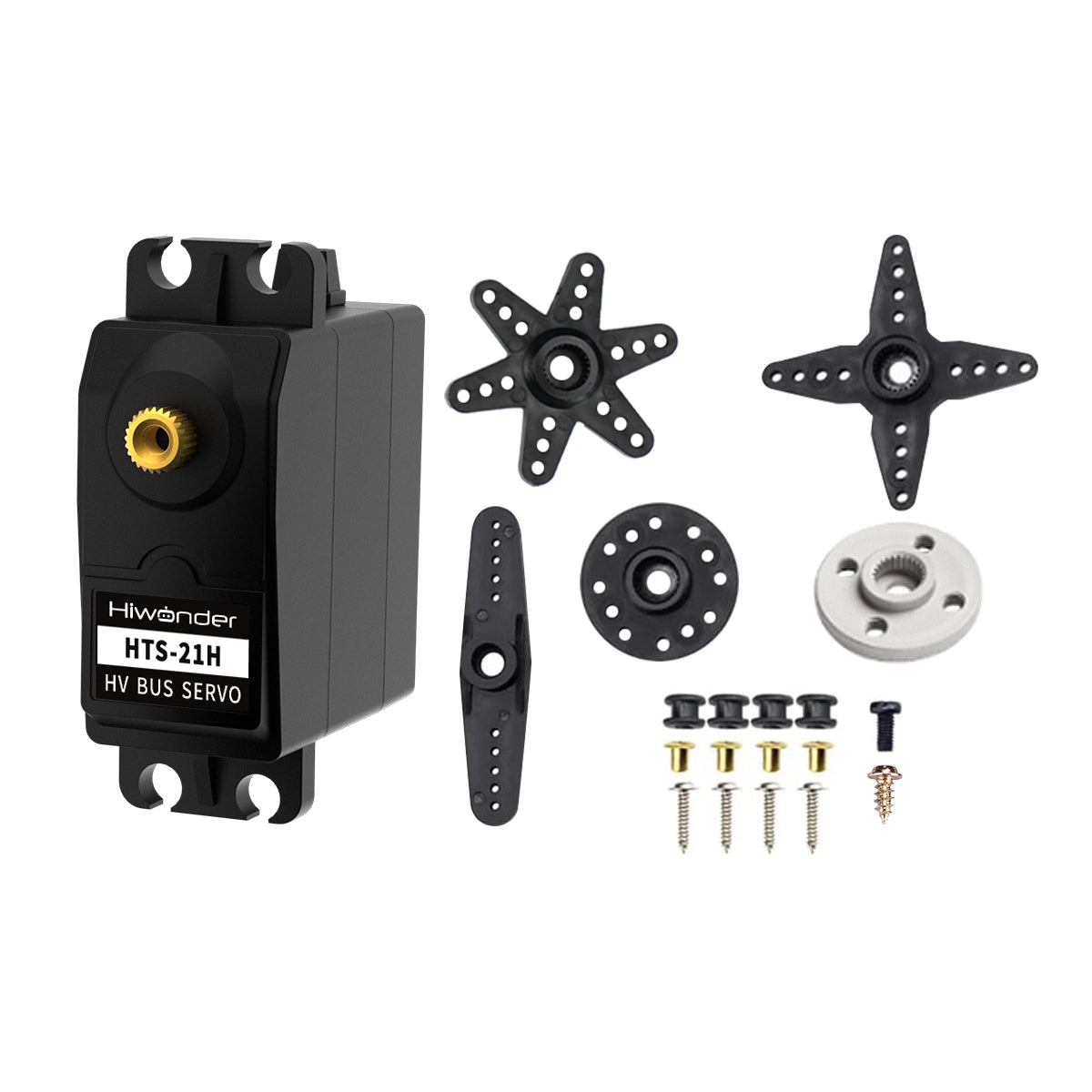
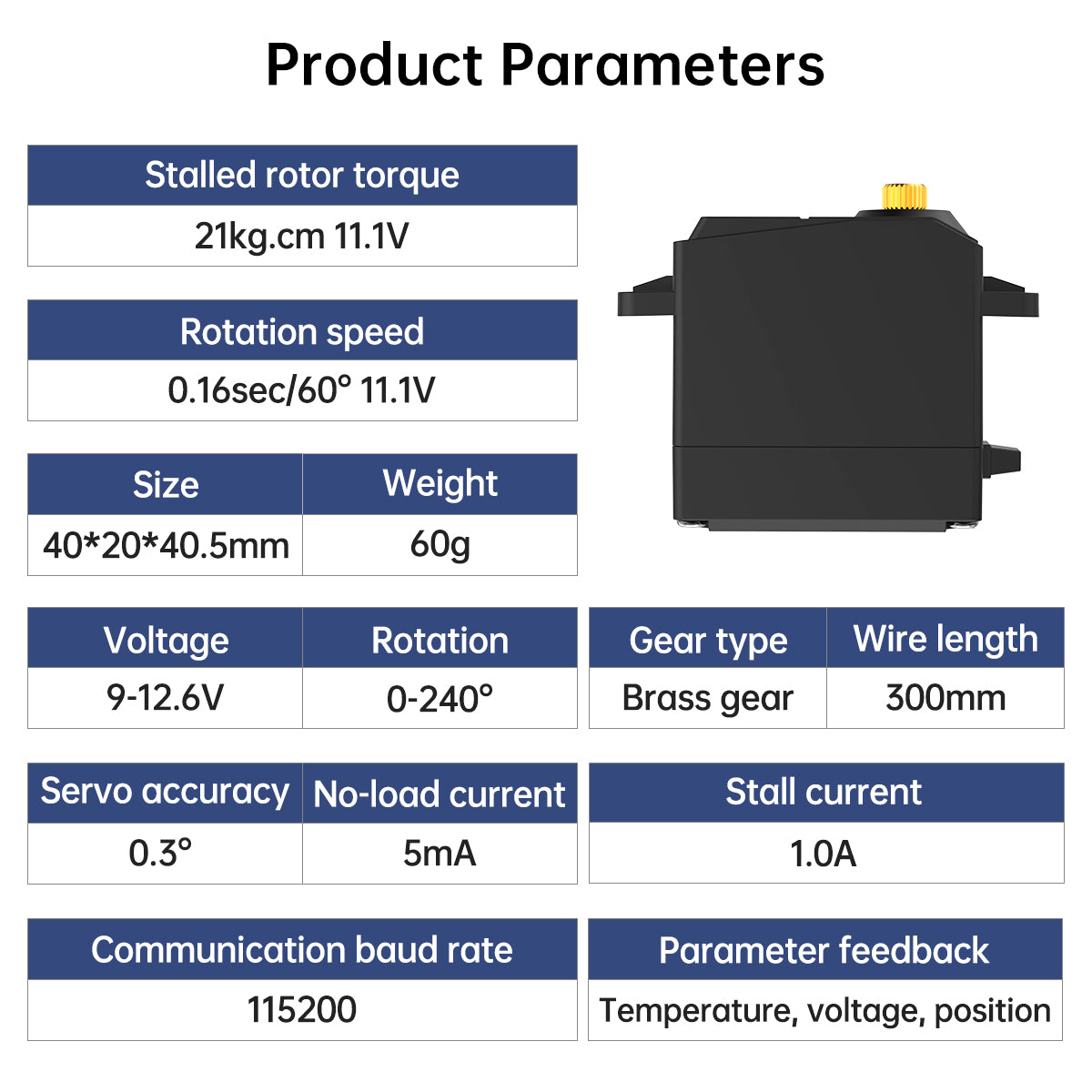
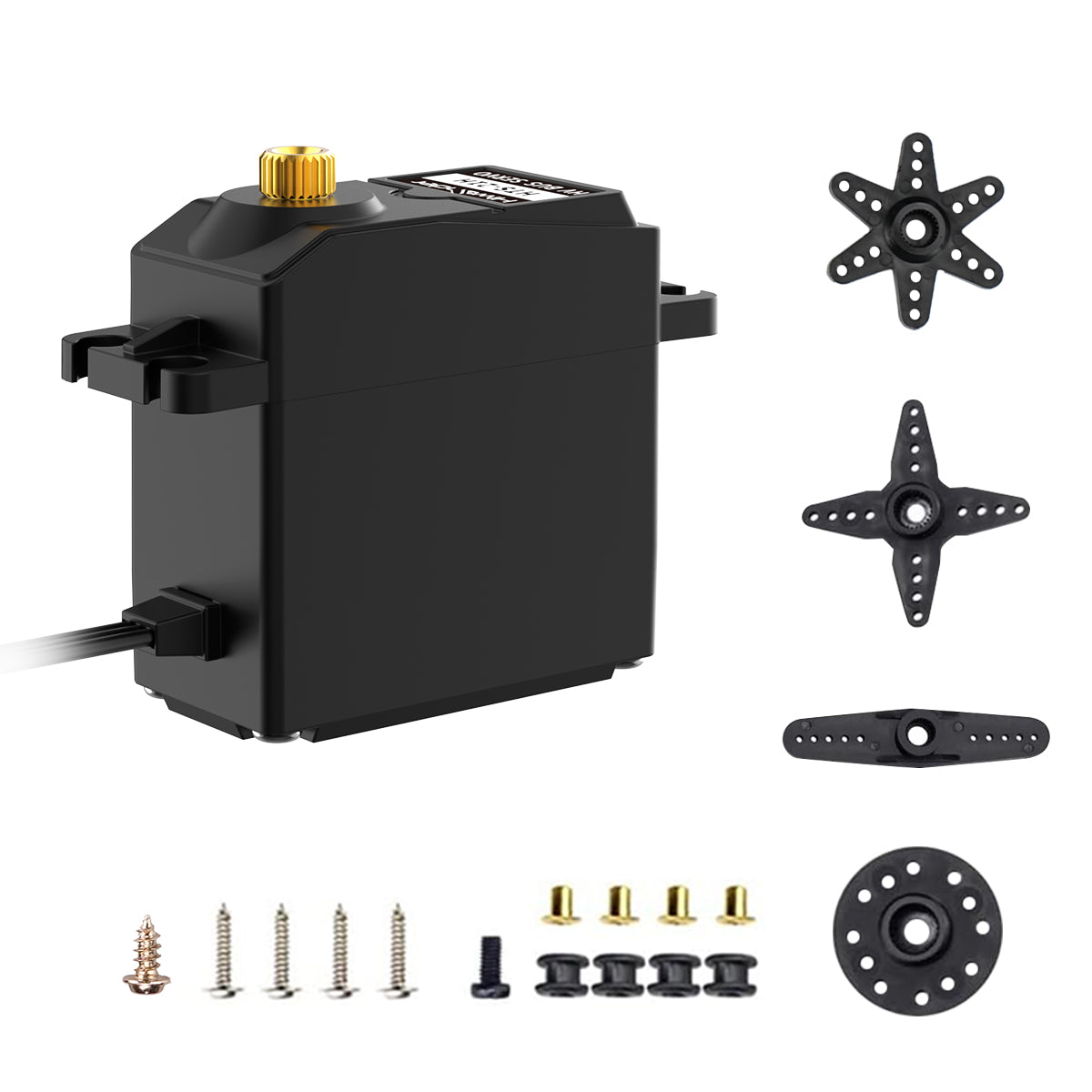
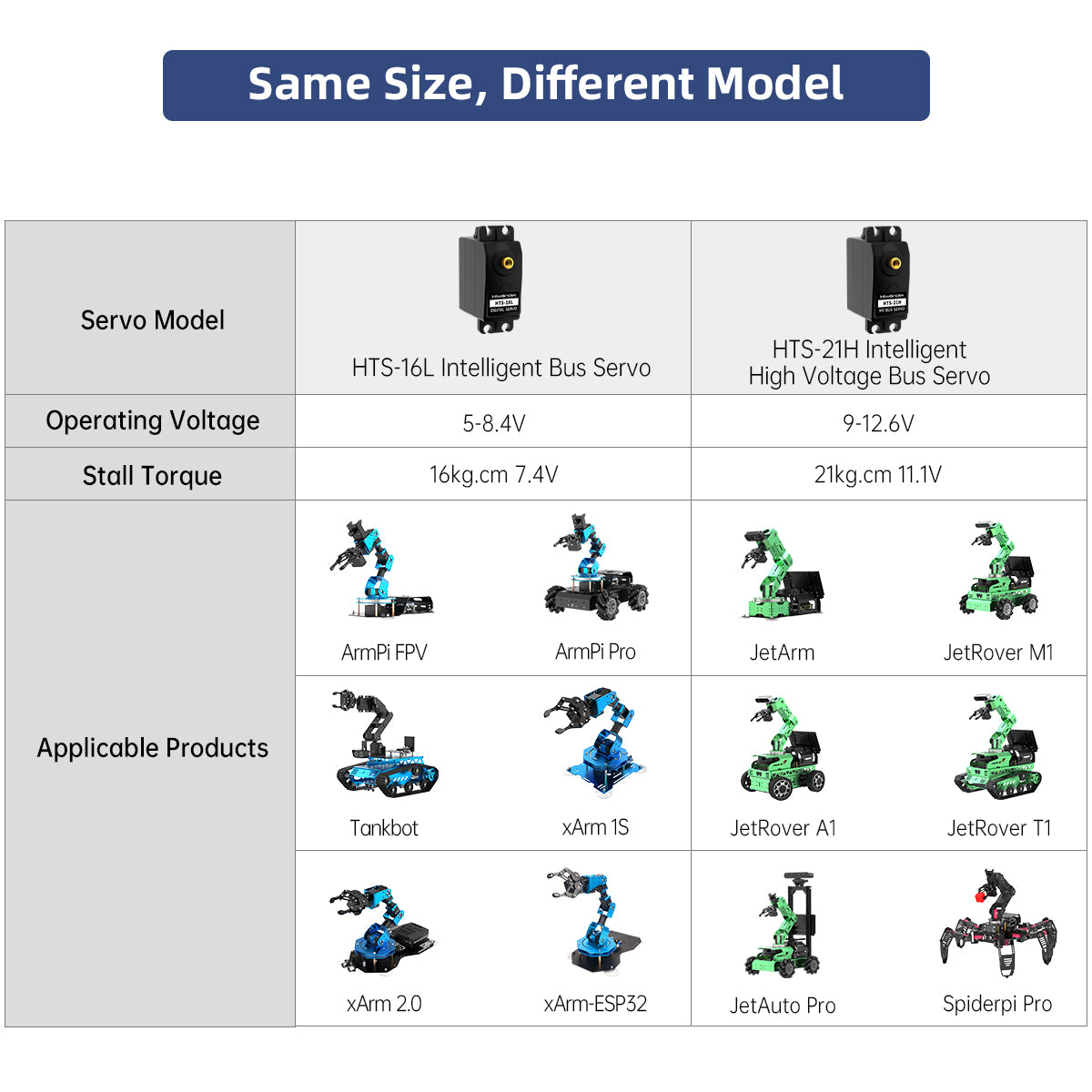
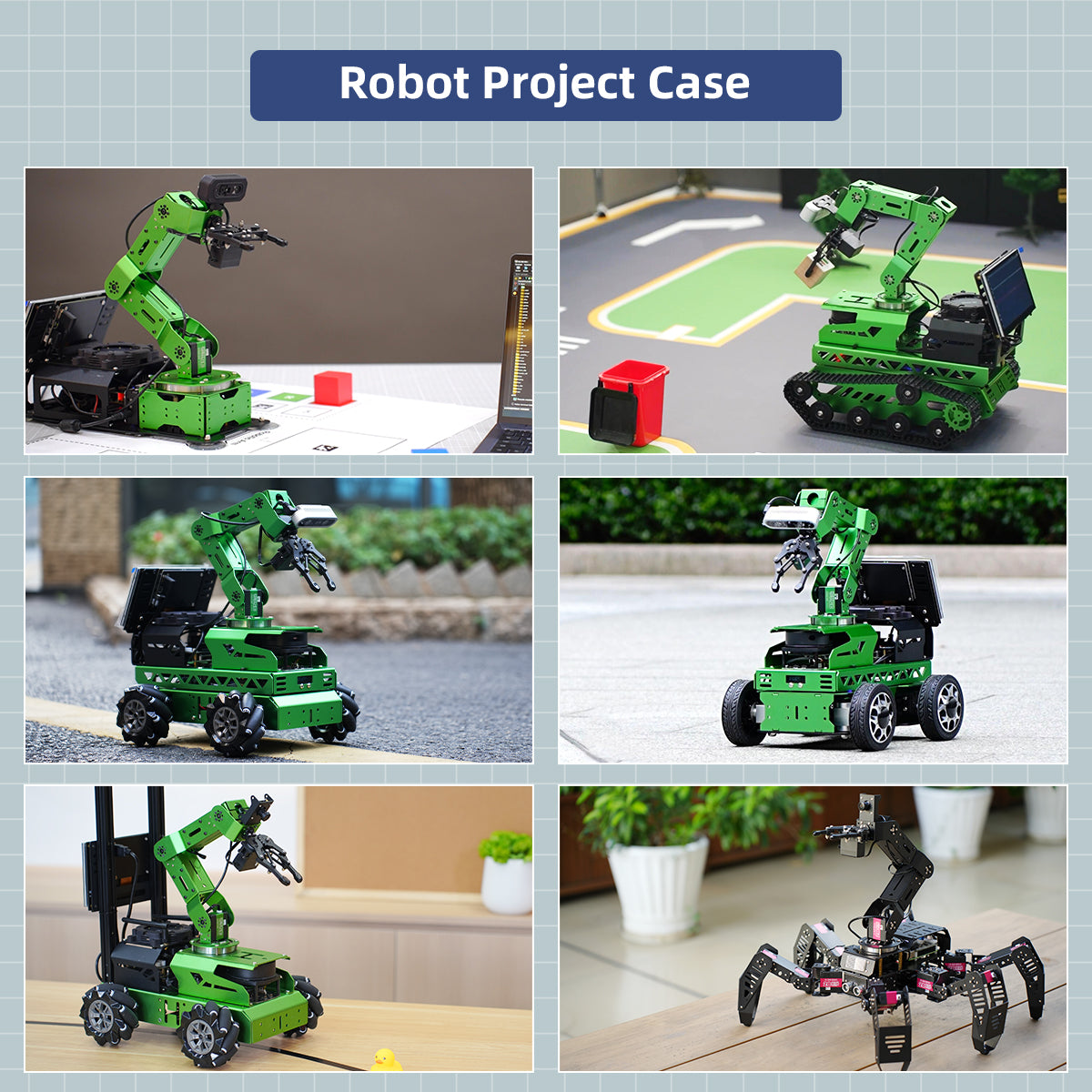
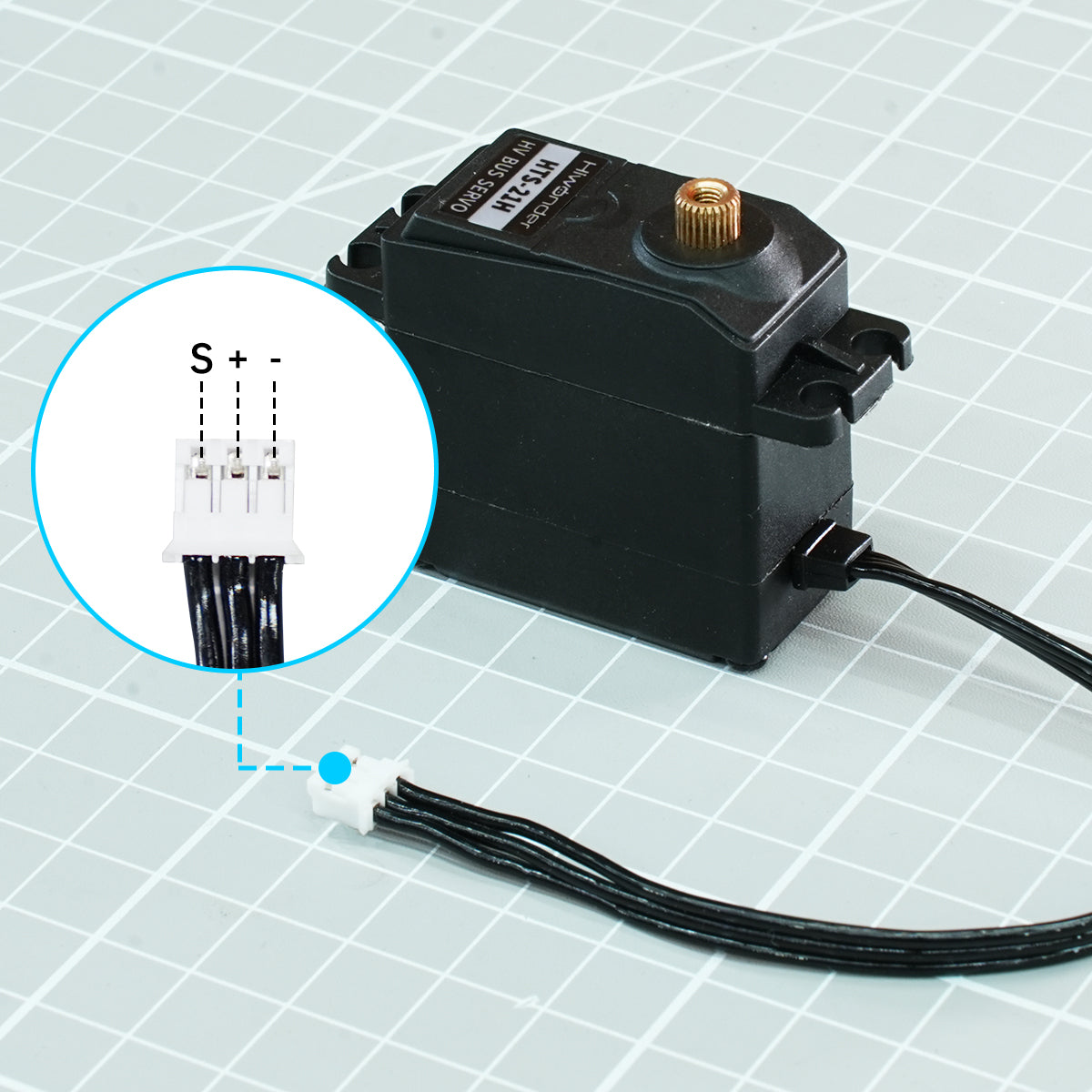
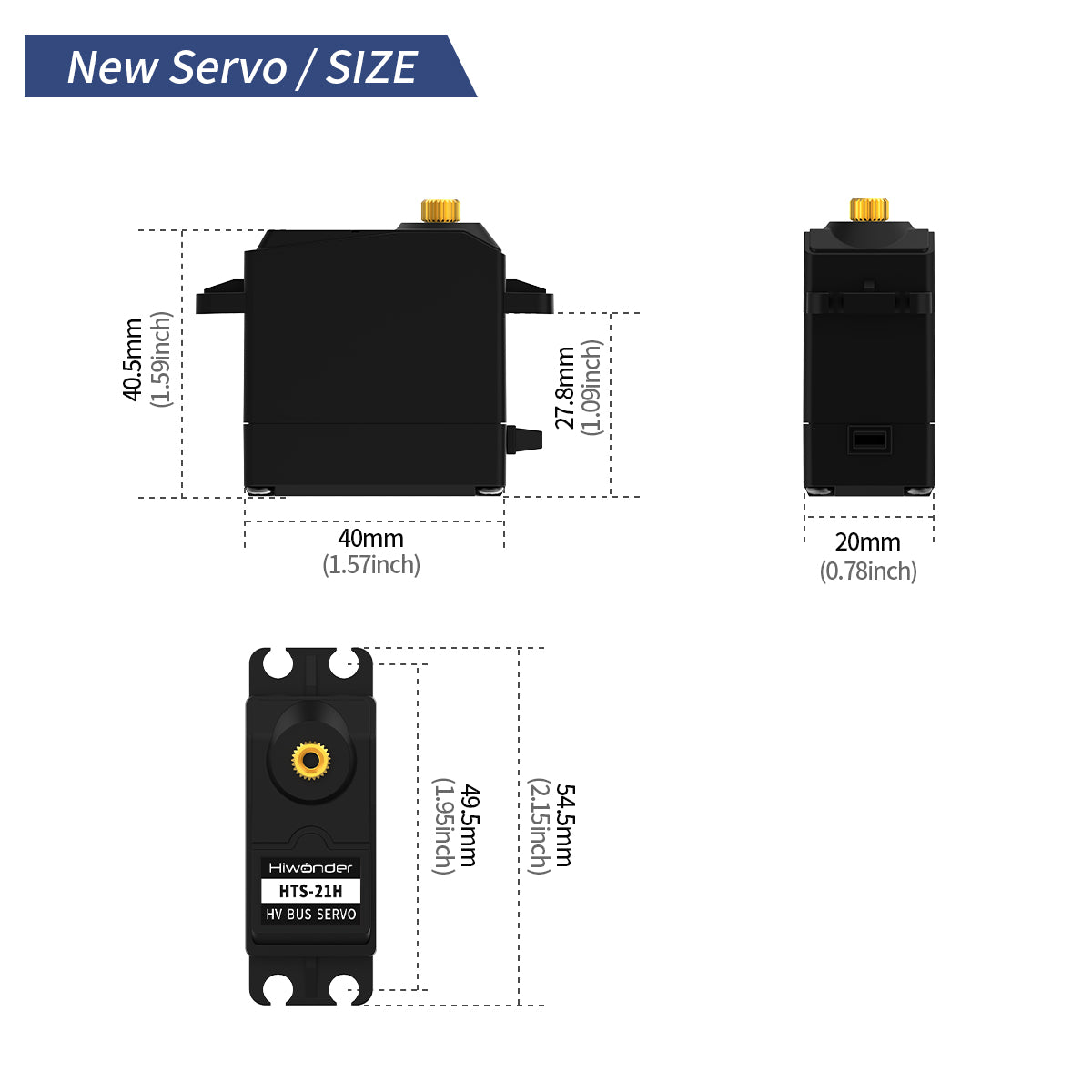
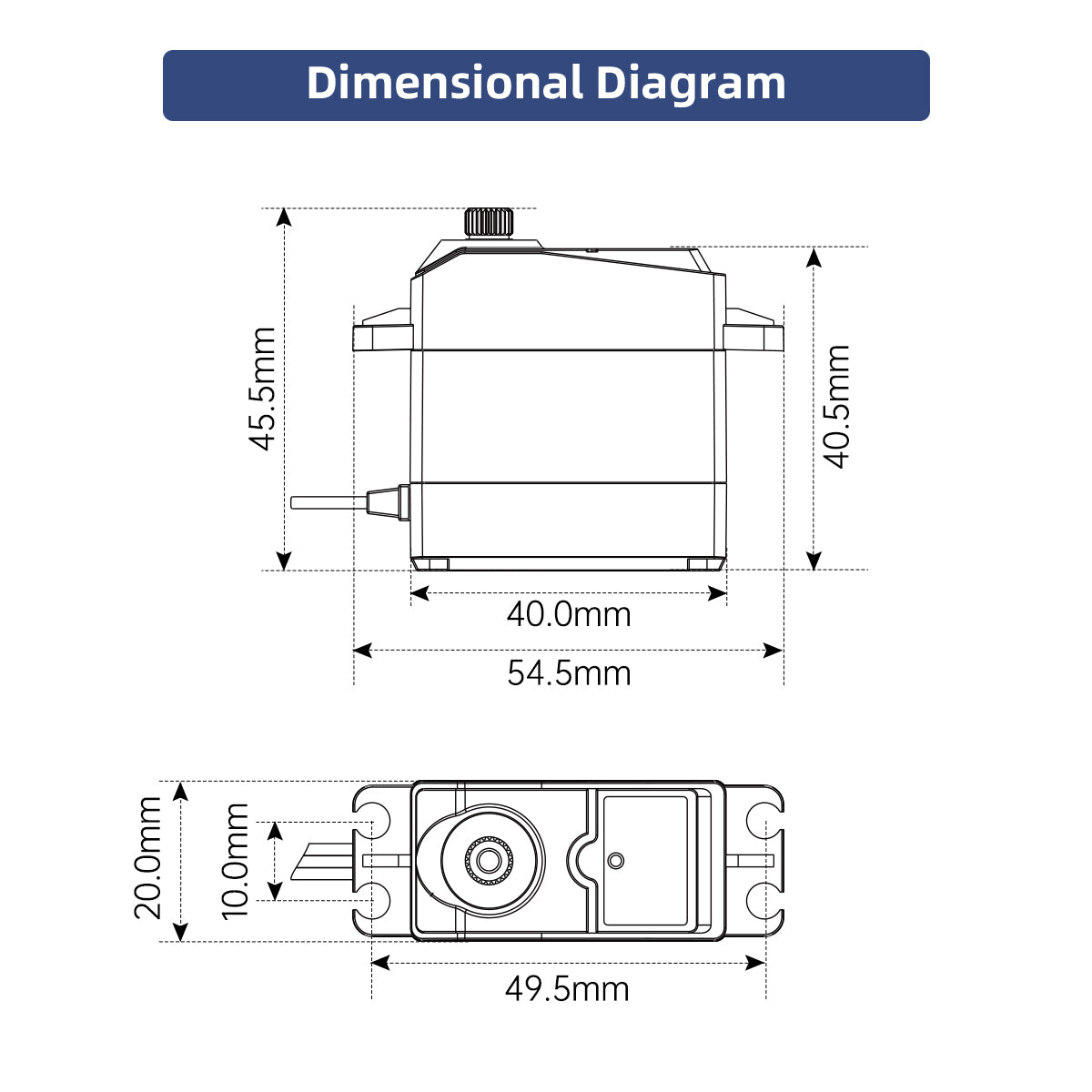
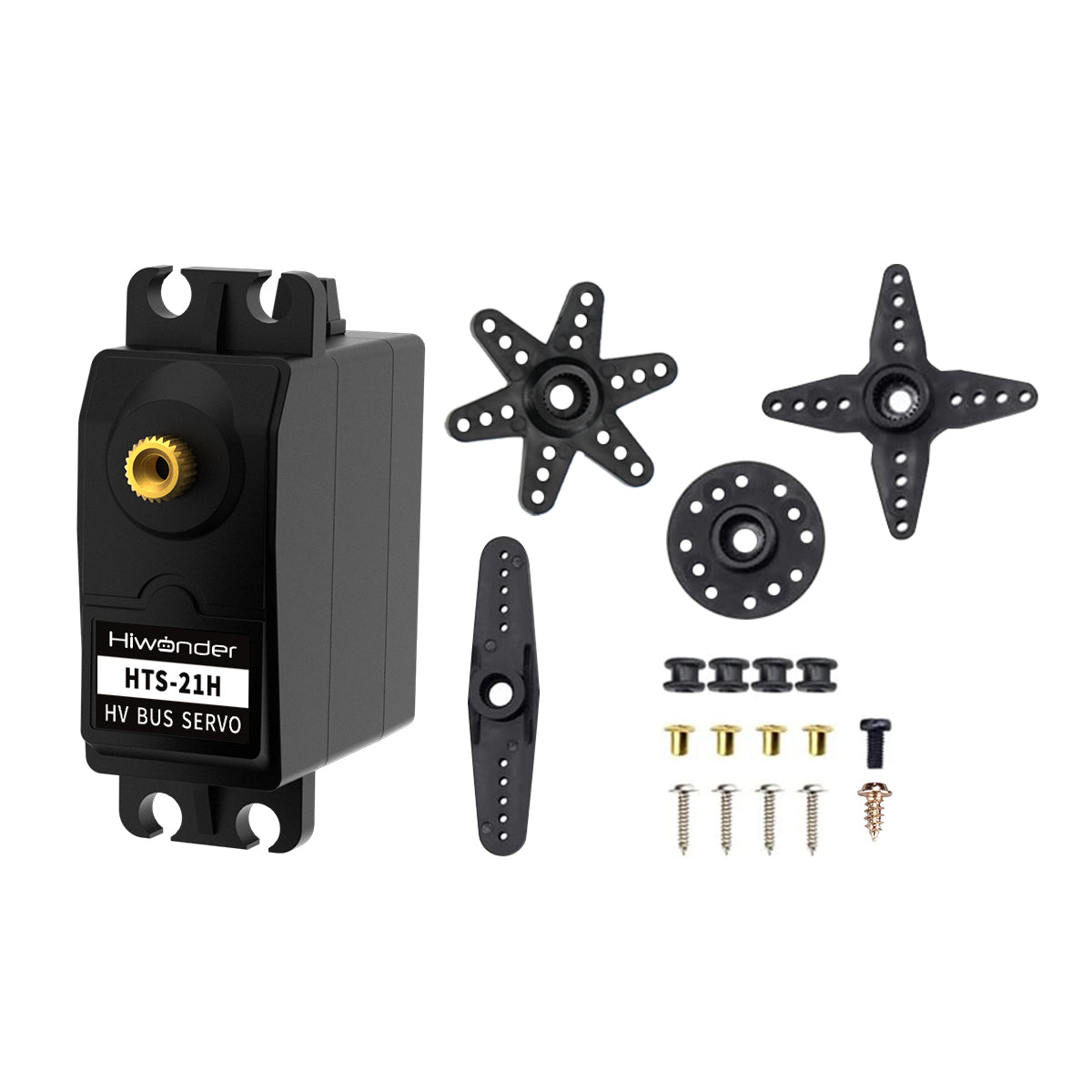
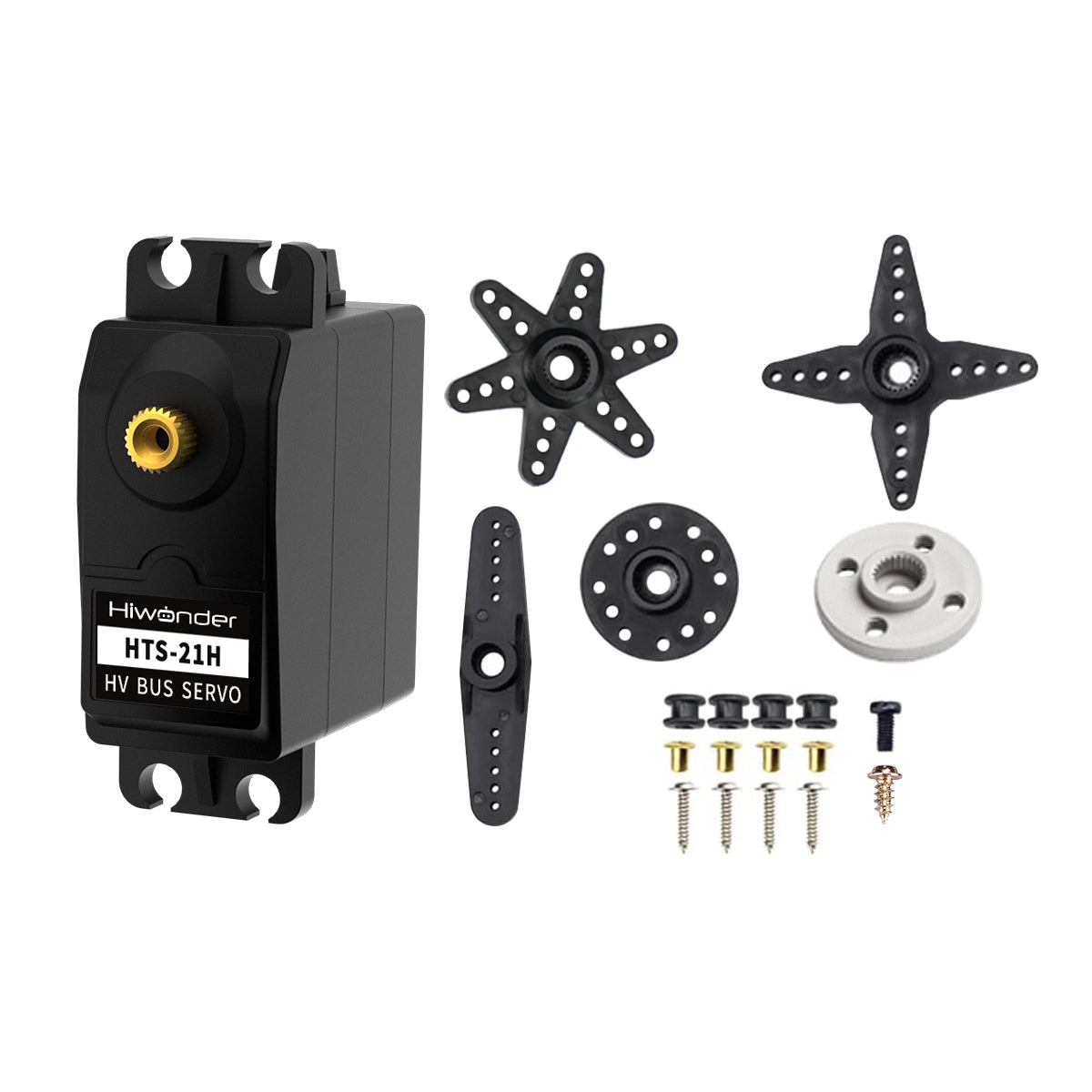
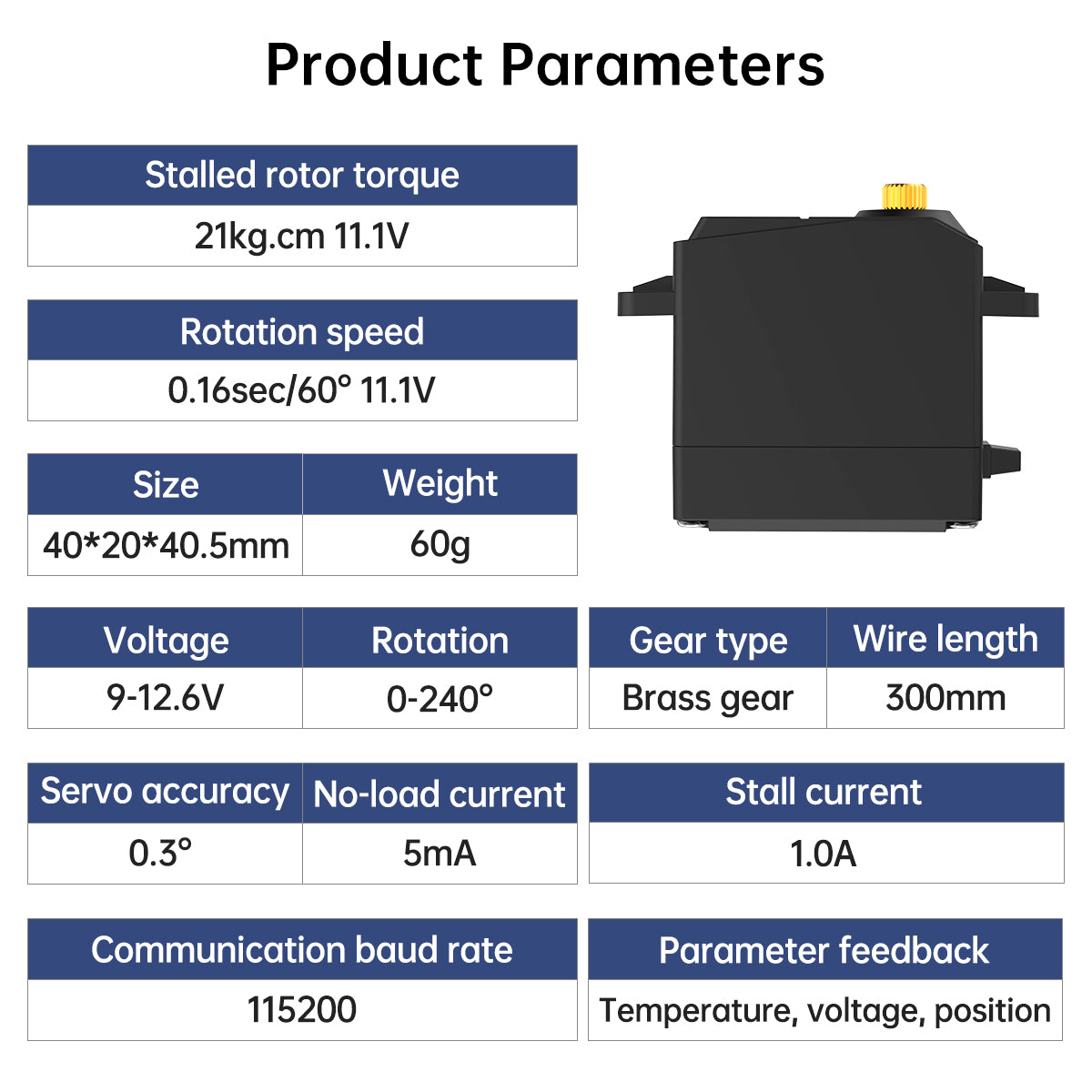
Hiwonder Serial High Voltage Bus Servo HTS-21H Anti-burning and Anti-blocking Intelligent Serial Port High Torque High Precision with Feedback Dedicated for Robot Gripper Claw
- Built-in Anti-burning and Anti-blocking Algorithm
- High Temperature Resistant Motor
- ID Identification Bus Communication
- Supports Servo Mode and Geared Motor Mode
- Temperature/Voltage Feedback and Angle Readback
- Description
- Specifications
- Accessories




Anti-burning and Anti-blocking Algorithm
The internal controller chip of the servo has a built-in anti-blocking algorithm, so that the servo will not be burned out due to stalling or collision, thus greatly extending the service life of the servo.

High Temperature Resistant Motor
The servo uses a high-temperature-resistant motor inside, which can ensure the safe operation of the servo in high-temperature environments and effectively prevent aging or burnout, thus extending the service life of the servo.

ID Identification Bus Communication
Each servo can be set with an ID number. The servo ID used to identify the servo is 1 by default and can be modified by yourself. The controller and the servo communicate using a single bus, and the communication baud rate is 115200.

Supports Servo Mode and Geared Motor Mode
In the servo mode, the rotation and positioning can be controlled within 240 degrees. In the reduction motor mode, it can rotate 360° continuously and control the direction and speed of rotation.

High-voltage Servo, More Energy-saving
For the traditional 7.4V servo, the 11.1V high-voltage servo can reduce the current by more than 60%, greatly improving the robot's battery life.

Temperature/ Voltage Feedback&Angle Readback
With temperature feedback and voltage feedback, the internal data of the servo can be understood in real time to protect the servo.The bus servo has angle feedback and supports angle readback to quickly read the servo angle and capture the position of the robot joints.

Metal Gears
The gears are made of stainless steel, which enhances the wear resistance and lifespan of the gears.

21KG High Torque
Powerful torque, adaptable to diverse mechanical claw scenarios.

Servo Debugging System
The debugging system allows you to control the servo's rotation for testing purposes, and monitor real-time servo data, including its position, voltage, and temperature.

Adjustable Parameters
In Debugging system, you can set ID number, working mode, rotation speed, position deviation, LED light, temperature alarm, stalling alarm and voltage alarm for servos.

PC Software Interface
We have added an angle readback function to the host computer interface. By manually adjusting the angle of the servo, angle reading and program entry can be performed, which can quickly realize robot programming.



Product | HTS-21H Intelligent High Voltage Bus Servo |
Weight | 60g |
Size | 40*20*40.5mm |
Operating Voltage | 9-12.6V |
Rotation Speed | 0.16sec/ 60° 11.1V |
Stall Torque | 16kg.cm 11.1V |
Rotation Range | 0°-240° |
No-load Current | 5mA |
Stall Current | 1.0A |
Servo Accuracy | 0.3° |
Control Angle Range | 0-1000, corresponds to 0-240° |
Control Method | UART serial port instructions |
Communication Baud Rate | 115200 |
Storage | Save user settings after power off |
Servo ID | 0-253 user can set, default is 1 |
Readback Function | Support angle readback |
Protection | Stall protection / over-temperature protection |
Parameter Feedback | Temperature, voltage, position |
Operating Mode | Servo mode and geared motor mode |
Gear type | Metal teeth |
Number of Teeth | 25T |
Product line | 30cm |
Applicable to | Special for mechanical gripper |

Weight | 60g | Applicable to | Special for mechanical gripper |
Size | 40*20*40.5mm | Operating Voltage | 9-12.6V |
Rotation Speed | 0.16sec/ 60° 11.1V | Stall Torque | 16kg.cm 11.1V |
Rotation Range | 0°-240° | No-load Current | 5mA |
Stall Current | 1.0A | Servo Accuracy | 0.3° |
Control Angle Range | 0-1000, corresponds to 0-240° | Control Method | UART serial port instructions |
Communication Baud Rate | 115200 | Storage | Save user settings after power off |
Servo ID | 0-253 user can set, default is 1 | Readback Function | Support angle readback |
Protection | Stall protection / over-temperature protection | Parameter Feedback | Temperature, voltage, position |
Operating Mode | Servo mode and geared motor mode | Gear type | Metal teeth |
Number of Teeth | 25T | Product line | 30cm |
Item | Specification |
Product | HTS-21H Intelligent Bus Servo |
Weight | 60g |
Size | 40*20*40.5mm |
Operating Voltage | 9-12.6V |
Rotation Speed | 0.16sec/ 60° 11.1V |
Stall Torque | 16kg.cm 11.1V |
Rotation Range | 0°-240° |
No-load Current | 5mA |
Stall Current | 1.0A |
Servo Accuracy | 0.3° |
Control Angle Range | 0-1000, corresponds to 0-240° |
Control Method | UART serial port instructions |
Communication Baud Rate | 115200 |
Storage | Save user settings after power off |
Servo ID | 0-253 user can set, default is 1 |
Readback Function | Support angle readback |
Protection | Stall protection / over-temperature protection |
Parameter Feedback | Temperature, voltage, position |
Operating Mode | Servo mode and geared motor mode |
Gear type | Metal teeth |
Number of Teeth | 25T |
Product line | 30cm |
Applicable to | Special for mechanical gripper |
This is the gripper servo in JetArm. If you just want a sturdy servo that responds to digital commands, then this is fine. However there are some limitations you should be aware of.
The unit has a similar serial protocol to the Robotis AX-12 but only runs at 115200 baud, not 1 Mbaud. This can be a problem if you have many servos, or want to update a whole set at approximately the SAME time (you have to dribble out all the commands ...).
Another undocumented property is that the readable data only updates at 15Hz. Given that there is a one cycle latency with commands, any external closed loop control only runs at 7.5Hz.
Finally, the servo claims to report actual potentiometer position but really seems to just echo the internally ramped command. You can set an angular target then physically block the motion of the servo, yet it will still report that it got all the way to the goal position.